Rubber Moulding Process Comparisons
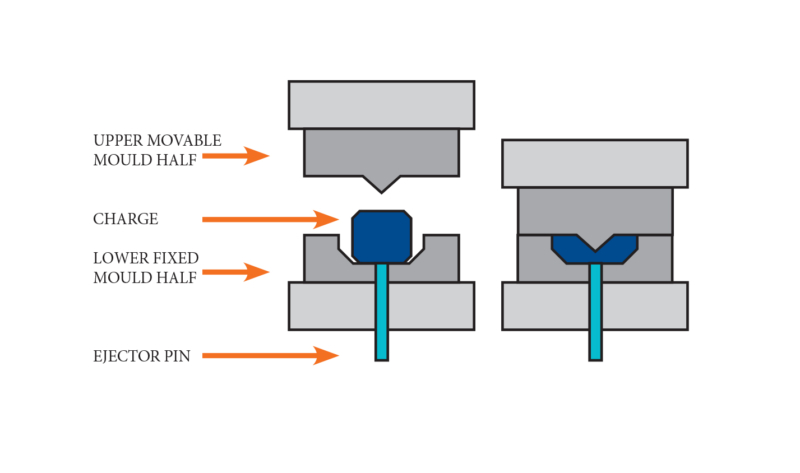
Rubber moulding process
There are various rubber moulding processes available. At DP Seals we believe that in most cases there is no need to go to full injection mould tooling and its typically high process control costs. Let’s take a closer look at each rubber moulding process in turn.
Compression moulding
The rubber material is placed in an open, heated mould cavity. The mould is closed and pressure applied to force the material into contact with the mould area. Heat and pressure are maintained until the moulding material has cured. This is shown on the diagram below.
The compression moulding process is useful for small to medium volume, straightforward and precision components, particularly where metal parts are required. It is also great for expensive materials like FFKM / perfluoroelastomers as there is very little wastage and it is the lowest cost tooling option.
Transfer moulding
The amount of moulding material is measured and inserted to the transfer moulding in, what is called, a transfer chamber. Once the raw material is in the chamber it is forced through runners and into the mould cavity or cavities. The mould remains closed until curing has taken place.
The transfer moulding process is a great technique for high quality, precision and intricate part designs in larger volumes. It is also particularly useful where less flash is required.
Injection Moulding
Components are produced by injecting raw material into a mould. Material for the part is fed into a heated barrel, then mixed and forced into a mould cavity.
This extremely versatile process is useful for varied sizes of components. However there are higher set up and tooling costs compared to transfer or compression moulding so it is ideal for high volume production of the same part where the per-unit cost can be reduced.
In summary
The combination of specialised compression and transfer moulding we offer allows us to cater for both high and low volume custom solutions achieving the excellent precision and quality for which we are known.
As outlined previously injection moulding is not something we offer but we’ll happily recommend a supplier should this be the best process for your particular requirements.