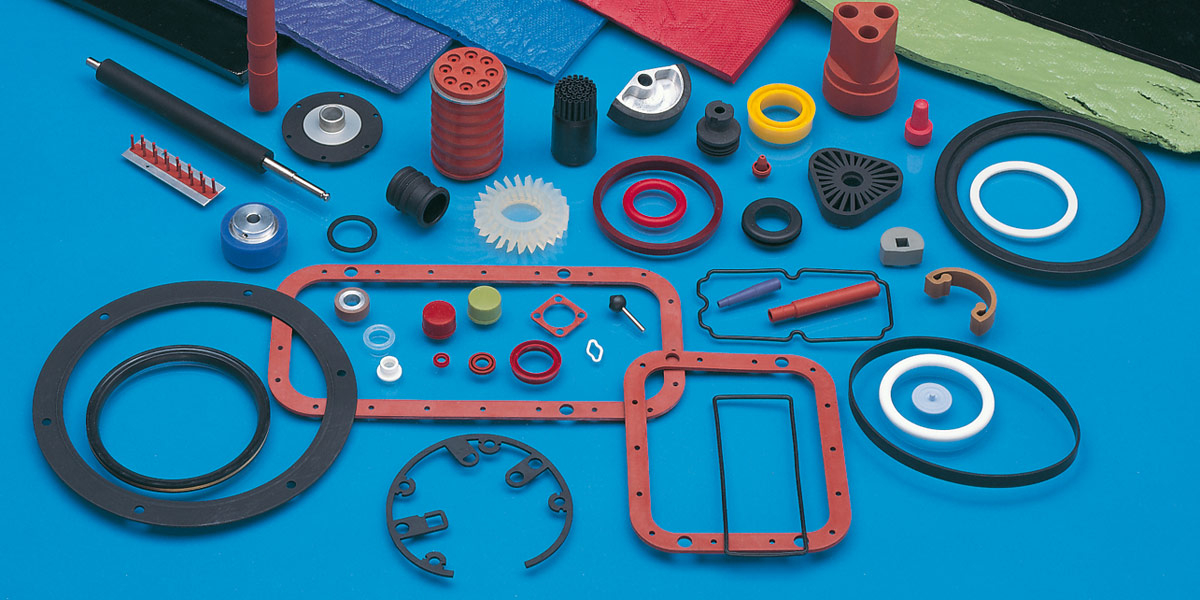
Natural vs synthetic rubber – They both have their place
In the natural vs synthetic rubber debate, Statista state that there were 15.2 thousand metric tons of synthetic rubber and 13.2 thousand metric tons of natural rubber consumed globally in 2018. Indeed, although synthetic rubbers can provide a myriad of property improvements both have their place in respect to relative performance characteristics and cost.
Natural rubber
Natural rubber can only grow in tropical climates and doesn’t age well. Most natural rubber is produced from the softwood Hevea brasiliensis tree, which is native to Brazil. However there are several other species of trees and shrubs from which natural rubber is sourced.
It has a high tensile strength, higher tear resistance, low odour, and is resistant to fatigue from wear such as chipping, cutting or tearing. It also has tack, which means it can adhere to itself as well as other materials. This is particularly the case for steel cord which makes it an excellent material for use in tires. Natural rubbers are also a very popular choice in the Subsea, Oil & Gas field particularly.
On the down side natural rubber has only moderate resistance to damage from exposure to heat, light and ozone. It also contains natural proteins which may cause allergic reactions when placed in contact with human skin for prolonged periods.
Synthetic Rubber
Synthetic rubber is artificially produced from polymers in different varieties to mimic the properties of natural rubber. So, for many countries, it is easier to use.
In general, synthetic rubber offers better resistance to abrasion than natural rubber, as well as superior resistance to chemicals, fluids, ozone, electrical heat and the effects of aging. Many types of synthetic rubber are flame-resistant, so it can be used as insulation for electrical devices. It also remains flexible at low temperatures and is resistant to grease and oil. Because of this synthetics offer excellent results for applications in extreme temperatures and corrosive environments.
For more detailed information about specific compounds see our data sheets and chemical compatibility database or call our material technologists.