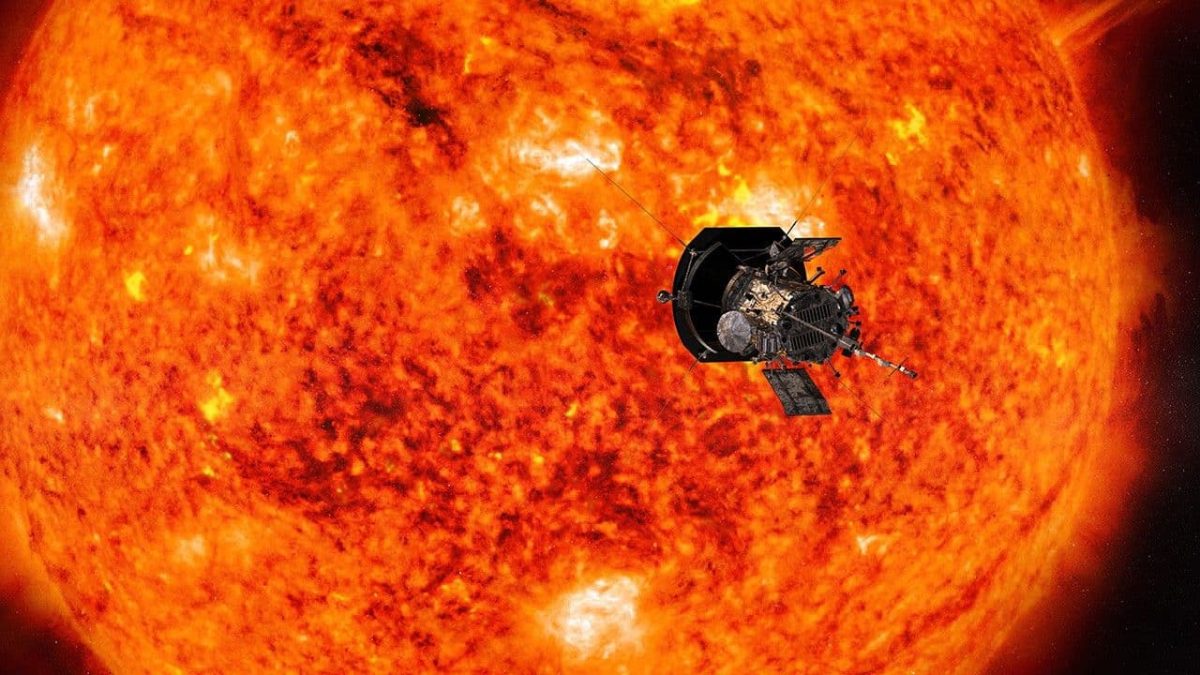
With the rise of privately funded space programs from the worlds super-rich elite, seeking to boldly go where no entrepreneur has gone before, space really is the place to be. Cheaper commercial methods of launching satellites and space missions have provided NASA with a much needed boost, and with Trump and Musk strapped in, colonisation of the moon and crewed missions to Mars now appear to be firmly back on track.
Obviously we’re surrounded by thousands of satellites. In 2024 there was an estimated 9900 orbiting the Earth, this figure seems to vary from source to source but one reckons there may be as many as 60k by 2030. All of these have an abundance of seals, gaskets and mouldings.
Much more glamorous is the recent success of NASA’s Parker Solar Probe (main image) which became the first spacecraft to fly through the corona – the Sun’s upper atmosphere, facing brutal heat and radiation. The probe has four instrument suites designed to study magnetic fields, plasma and energy particles and image the solar wind. These are protected by a 113mm thick solar shield made of composite material. Even with this, the forces that seals and gaskets had to withstand are massive compared to anything found on our own planet.
The hazards of space
Wherever there is machinery, electronics, communications and equipment operating in hazardous environments there will be a requirement for custom rubber mouldings, gaskets and seals made from highly-specialised materials. None more so than in the vacuum of space where hazards can come thick and fast. From extreme high and low temperatures, radiation, atomic oxygen, ultra violet and electron particle radiations, pressure and an endless assault of micro-particles of dust travelling at speeds of up to 27km per second. These MMODs (Micro-Meteoroid and Orbital Debris) are small pieces of orbiting trash and galactic ice. The damage of these hyper-velocity particles can be devastating.
For future missions to the Moon there is a further barrier to overcome. Previously encountered by astronauts on earlier missions who’s space suits became coated with dust as they collected lunar soil. Commonly referred to as Moon dust. Lunar Regolith is a grey fluffy powder that at the microscopic scale is jagged and sticks like the proverbial to everything – including itself. Not only representing a health hazard, it is prone to hanging in the low-gravity atmosphere when kicked up by rocket motor thrust or other lunar activity, it’s fine grittiness wearing down tools, seals, joints and equipment.
Credit: NASA
Where are rubber seals, gaskets and
mouldings used in space
Rubber components can be found in the following applications used in satellites, space and launch vehicles:
- Docking Seals
- Fuel Feed-lines
- Valves
- instrumentation
- Propulsion Systems
- Thrusters
- Around structural parts
- Gyroscopes
- Solar Panel Arrays
- Reaction wheels on micro-satellites
- Space Suits
Astronauts wear Prada
Well not quite yet, but Axiom and Prada have got together to modernise NASA’s trusty suit for their historic Artemis III mission in 2026, marking humankind’s first return to the moon since 1972. Creating a far more flexible, one size fits all unisex design with an operational use of up to 8 hours and the ability to include specialised tools. The current 1974 NASA suit had a ticket price of $12m so you won’t find many of them hanging in the wardrobes of even the most ardent of fashionistas, but the latest Prada/Axiom model is coming in at a fraction of that cost, so who knows – in generations to come you may find them hanging next to your skiing jacket.
Todays spacesuits are marvels of engineering, relying heavily on advanced materials as well as chemicals to keep astronauts safe and able to operate in the vacuum of space. The prime rubber material used here is Neoprene. Used in the gloves, boots and various seals around the openings of the suits. Neoprene is resistant to water, oils and chemicals and remains flexible at low temperature, ideal for space use – as indeed it is in subsea applications where similar hazards can be encountered.
What rubber materials are
best suited to space
Materials will need to possess excellent sound and shock absorption, require minimum maintenance with no need for lubrication between parts and a high-endurance threshold under extreme stresses.
- Butyl rubber has been used in reaction wheels which are used to stabilise and manoeuvre satellites in orbit without the use of fuelled propulsion systems.
- Specially blended EPDMs that are primarily developed for propellants.
- FFKM for high and low temperatures combined with excellent resistance to chemicals.
- Silicones work better at low temperatures, regular elastomers become too firm leading to leakage, they are very durable in vacuum environments.
- Radiation can cause issues in Polymers and natural rubbers.
- The durability of rubbers to radiation is highly dependant on the fillers that are added to the compound.
DP Seals have an excellent background in custom materials for the Aerospace industry having supplied to leading engineering teams across the world. From nitriles, neoprenes and silicones through high-performance FKM and FFKM to cutting edge polymers like silicone perfluoroelastomer and nanotech rubbers, DP Seals uses its 40-year plus experience in rubber chemistry to work with compounders to develop the right blend whatever the application.
https://dpseals.com/materials/rubber-materials-expertise/
DP Seals The Unseen Advantage
DP Seals adds value at every production stage, especially during the design phase.
We can add value in all the following areas:
- Ultra-high pressure and vacuum sealing
- Low outgassing
- Expertise in FFKM
- Chemical resistance
- Radiation compatibility
- Electrical insulation
- Co-moulded and conductive rubber
- Combined in-tool metal and rubber mouldings
- Low friction and wear
- Fluorination
See our Product Development page on our website.
https://dpseals.com/services/the-design-process/
The last word
Although the future of commercial space travel seems to be firmly in the grasp of the worlds super rich – it should be remembered that not so long ago, one man and his intrepid, resourceful dog managed to make that trip to the moon and back in just a day.
Beat that President Trump.
To discuss any requirements you may have or to find out more about DP Seals range of services get in touch.