Extreme Temperature Seals
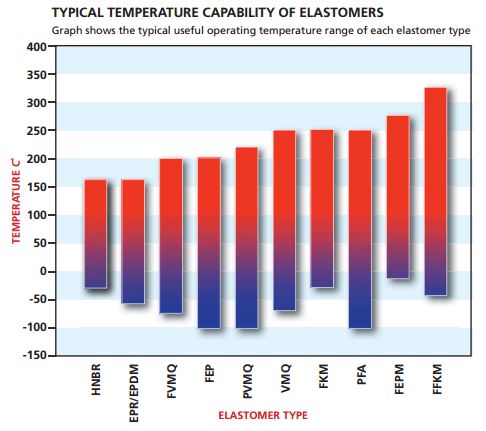
When designing extreme temperature seals, gaskets and mouldings use these top tips based on DP Seals 40 plus years experience in the industry and feedback from our design engineer customers.
Exposure to temperature is a significant area to be aware of when making material choices. Here are some top tips to think about when designing rubber parts.
Tip 1: Consider temperature in balance with other performance characteristics
When designing your custom rubber seal, gasket or moulding think about all types of exposure that the part will come into contact with. So whether you need low temperature flexibility or high temperature resistance, this must all be balanced with the need to resist certain fluids, for example fuels and solvents.
Tip2: Get expert advice and support
Engineers told us that they need to think about the performance characteristics of rubber material at different temperature ranges including things like out-gasing, chemical background, thermal expansion and safety in fault conditions.
This is, of course, an important area and in the following diagram you can see how certain materials compare with low and high temperature ranges.
It is clear that the right base polymer is key, however, through bespoke compound formulation we can pinpoint and provide the best material for your application performance. At this stage we’d recommend getting expert advice from your manufacturer. DP Seals has over 40 years experience in material technology and we can help you formulate exactly the right blend. Talk to your manufacturing partner as early as possible; good communication can save a lot of time and money in the long-run.
Tip 3: Rubber can operate in temperature ranges you might not expect
As you can see from the previous diagram some Silicones can perform at minus 100° degrees C and even lower. Right at the other end of the scale they can withstand excursions to over 300° degrees C, depending on the grade used and compound formulation.
One of the most extreme challenges we have overcome was a requirement to have good fuel resistance and to get down to below minus 50 degrees C. After sampling and subsequent witnessed testing we managed to get a low temperature HNBR down to below this minus 50 with a good seal maintained.
Tip 4: You might need to make some trade-off
With most organic materials there is normally a trade-off for each end of the scale. For example we can compound a Nitrile rubber to remain flexible at low temperatures down to -40°C and more. We can also formulate a grade that is good at the top end of say 120°C, but we cannot always help with both requirements together, so again material base polymer choice is critical.
Summary
In this article we’ve touched on some of the key things engineers should consider in respect to temperature when manufacturing custom rubber, seals, gaskets or mouldings. We’ve outlined:
- The importance of considering temperature in relation to other things the part could be exposed to.
- The benefits of getting expert advice.
- The fantastic ranges of temperature that rubber can operate in.
- The performance characteristics of material at different temperature ranges and the need to sometimes make trade-offs.
However, temperature is just one consideration and shouldn’t be seen in isolation. Get in touch to discuss your requirements.