The Cleaning Process
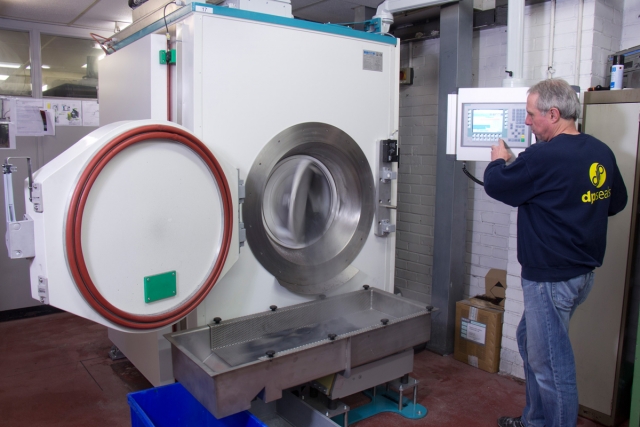
The Early Days
Our cleaning department has evolved over the years and become a major part in our production process. Steve Collinson started in the cleaning department 22 years ago and recalls the early days. He had an industrial tumble dryer, two slow speed rotating tub machines and very limited sizes of ceramic media. In addition there was one N-180 cryogenic deflashing rubber machine using liquid nitrogen and aluminium oxide balls. This machine had an on/off switch and limited speed control. That was it!
Steve would load the machine, leave it for about 15 minutes and hope that everything was okay and not smashed up when he returned. Next he would shovel out the seals, gaskets or mouldings complete with the cleaning balls and very carefully separate the two.
Entering the computer age
The TS10 has the ability to spin the drum at much faster speeds up to 6000 rpm. Liquid Nitrogen is sprayed into the tank until it has reached the desired operating temperature which is, on average, -75C. This freezes the product, at which point media is blasted into the tank to remove excess flash. Once the process is complete the media is automatically separated and passed back into a storage tank. At this point the hatch can be opened and, whilst the drum rotates very slowly, the product slowly empties, saving a huge amount of time.
A flexible, modern approach
DP Seals recently added an even newer cryogenic machine and this has more than doubled the throughput of work. With the evolution of different cleaning medias we are able to clean very small, fragile parts in these two cryogenic machines.
Whilst these machines have transformed the control and speed of cleaning Steve still uses the variety of rotating tub machines to provide greater flexibility on how every product is cleaned.
Over the years the cleaning process at DP Seals has improved significantly and we’ll continue to invest to keep ahead of the game.