Rubber Moulding Quality Tips
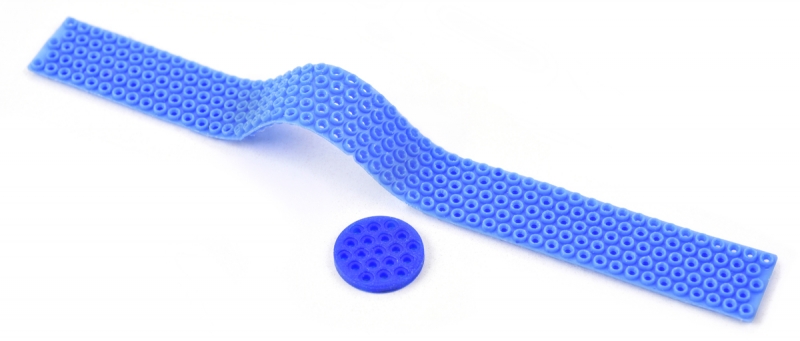
Rubber moulding quality considerations are a significant area to be aware of when designing custom rubber seals, gaskets or mouldings so here are some top tips for your consideration. They are based on speaking with engineer customers and DP Seals 40 plus years experience and expertise in the custom rubber seals, gaskets and mouldings business.
TIP 1: Think about and prioritise the different aspects of quality before talking with your manufacturer
Prioritisation is key and one of the best tips I can give design engineers is to really think about what they mean by quality before discussing this with their manufacturer. Quality could mean less flash, split line, integrity, surface finish, appearance or even rubber mix. Prioritising your requirements will really help in discussions about material selection and technical considerations.
TIP 2: Understand where you do need extra quality as well as where you don’t!
Following on from the previous tip I think it’s important to review the overall technical elements of the part like fit and function. Review elements such as hardness, material choice, tolerance criteria, surface finishes and feed point positions to build a strong picture of where you do and don’t require extra quality.
Tip 3: Closely consider the capability and credentials of your manufacturing partner.
A custom made rubber moulding can sometimes really push the boundaries with, for example, the need for tiny holes, radius or lip features. All of these details are very often critical to how the component functions in application and this may necessitate the requirement for no ‘flash’, ‘feed’ points or ‘split’ lines in these areas.
Thoroughly consider the toolmaking, moulding, prototyping, manufacturing, quality and certification standards of your manufacturer. At DP Seals, for example, it is our patented ‘transfer’ moulding system and first class approach to quality that makes many of the demanding requirements we’ve described possible.
TIP 4: Get your manufacturing partner involved in the process as early as possible
The most important thing for a manufacturer is to have the opportunity to be involved early in the process. At DP Seals, as a team with over 40 years experience we can add real value at this stage through our expert knowledge in material selection, technical experience, prototyping and helping with all the points we’ve made in this article.
Summary
In this article we’ve touched on some of the key things engineers should consider in respect to quality when designing custom rubber, seals, gaskets or mouldings. We’ve mentioned:
- the importance of prioritisation
- thinking about different quality requirements for different aspects of the part
- sharing what you don’t need as much as what you do need
- choosing a manufacturer with the required credentials and capabilities
- involving your manufacturer early in the process
Of course we’ve largely written about quality in respect to finish of the part in this article but we like to consider quality throughout the whole process. From initial discussions through to your manufacturing partner checking that you’re happy with the solution after receipt of the parts. Quality should run throughout.
It’s also important to remember that quality is just one consideration and shouldn’t be seen in isolation. Every part is different with its own unique features.
Get in touch with us now to discuss your requirements further.