Rubber Mouldings Checklist
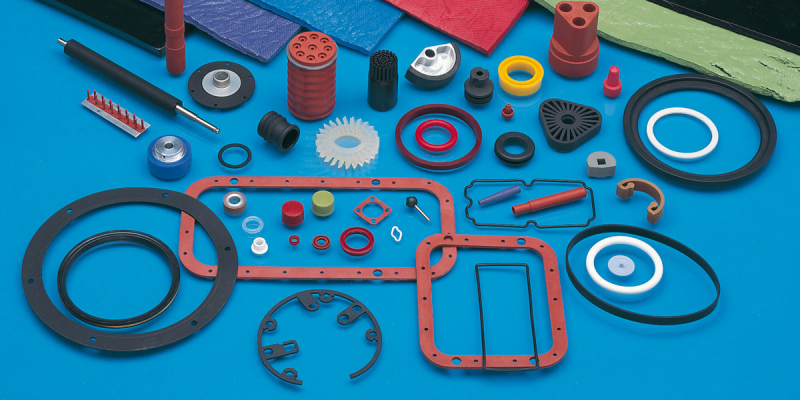
The importance of early communication with your rubber seal manufacturer
Producing a rubber seal, gasket or moulding for your product requires significant collaboration between engineers, production teams, material technologists and the manufacturer. This rubber mouldings checklist for engineers has been designed to ensure communication is as effective and smooth as possible.
The time and cost pressures on engineers today are higher than ever. By communicating early and thoroughly with your chosen manufacturer you will have the best chance of saving time, reducing costs and gaining a competitive advantage.
On the contrary leaving your choice of material, profile and manufacturing process until too late could force you into choosing a standard product which compromises product performance. Alternatively, last minute manufacture of a specialised moulding could result in delays to market entry and higher costs overall.
For an engineer to communicate clearly it is crucial to explain the thought process behind the work, be it with your team, business or clients. We trust this handy checklist will play a part in helping you do just that.
Key Questions & Considerations When Producing a Rubber Seal, Gasket or Moulding
What needs sealing?
The answer to this question helps point the way towards choice of an injection, transfer or compression moulding process. Some key considerations include:
- What is the part geometry? Consider use of videos and pictures in addition to part drawings to help explain requirements to your manufacturer.
- What other materials will be part of the application?
- What is the overall mechanical arrangement of the application in which the seal or moulding will operate?
Why does it need sealing?
Rubber comes in a wide variety of forms and compounds, all with different performance characteristics, and this helps to make initial material choices. Consider the following:
- What problems are you trying to solve? Vibration, Leakage, Protection (Dust, Magnetic interference, Chemicals, Water, Solvents)
- Is there a requirement for rubber to metal bonding or could this help strengthen the part design?
What timescale are you working to?
Understanding your project goals helps ensure you get your product to market in a timely and efficient manner. Consider the following:
- 3D printing & rapid prototyping can help in identifying faults and allow you to try out different versions of your seal, gasket or moulding. By doing this, the development process can be sped up significantly.
What are the budget parameters?
It is important to understand your short or long term planning approach to help get the best return on your investment.
- Choice of material may increase upfront costs but help improve product lifespan to deliver an improved ROI.
- Is there a requirement for the re-use of moulds & tooling?
- Volume/Quantity of parts, repeat order requirements and batch consistency into the future.
What are the expected performance characteristics of the application?
It is important to understand all the parameters that might influence your seal or moulding including:
- Type of motion experienced by the application. Which of the following conditions will the seal work under and for how long? Static/Dynamic.
- Displacement and flexibility in respect to rubber hardness characteristics.
- Required Tolerances – only where required and avoiding defaulting to metallic, machined or turned parts.
- Fluids. What fluids will the seal be exposed to in both its primary use but also when being cleaned or lubricated, for example?
- Temperature. What temperature ranges will the seal need to work under, both hot and cold? What is the importance of temperature performance in relation to other factors?
- Contaminants. What abrasive external contaminants might the seal be exposed to?
- Ozone. Will there be a presence of ozone which can attack rubber?
- Processes. Will the rubber be exposed to processes such as sterilisation by gas, autoclaving or radiation?
- Light. Will the rubber be exposed to ultra-violet or direct sunlight?
- Out-gassing. Will the rubber be exposed to the potential for out-gassing in vacuum applications?
- Water. Will the seals be exposed to water?
- Pressure. What pressures will the seal work under, both low and high?
- Friction. What level of friction will the seal be exposed to?
- Quality. What quality of finish is required and what are the key priorities? Will all elements of the part require the same level of quality?
We hope you found this article useful and have produced the Engineers Checklist should you require a handy reference or want to share with colleagues. Download it for free now.